Our
strong quality assurance policies, in concert with our
corporate philosophy of "Zero Waste Manufacturing"
have resulted in unprecedented
perforformance ratings
and that has given us the ability to meet our Customer's must stringent demands.
In order to provide a complete picture of our policies,
we have included our complete Q.A. Manual for your perusal.
Scope:
The purpose of this document is to create an overview of the systems and
procedures required to support our greater corporate philosophy. The
essence of this philosophy being the successful implementation of
Environmental and Social commitments that are clearly advancements to the
"standards" set by our industry. It is our belief that a strong
Quality Program is an essential element in this process and therefore, the
following QA Policy will assist us in achieving these goals through the
implementation of:
1.0 Organizational Chart:
President, CEO- - - - - - - - - - Art Frengel
|
|
|
Accounting- - - - - - - - - - - - - Renee Frengel
|
Machining Dept. Manager- - -Brian Curtis
|
|
Safety Director- - - - - - - - - - Art Frengel
|
QA Manager - - - - - - - - - -
Jason Frengel
|
|
Fabrication Manager- - - - - - -Taisun Tony-Williams
|
Shipping- - - - - - - - - - - - - -
Placido Lopez
|
|
Purchasing- - - - - - - - - - - - -Jason Frengel
|
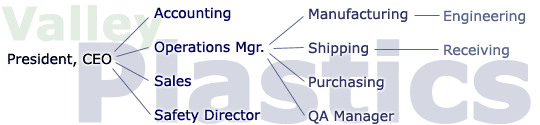
Below is a brief overview of each position's job responsibilities..
President / CEO
All legal correspondence, Asset management, Creates
policy
Accounting
Receivable / Payables, P/L reports, Cash Flow maintenance,
Payroll
Operations Manager
Is responsible for all aspects of Manufacturing, including;
Quotations, Customer communications, Scheduling , Personnel.
Sales
Creates marketing plan, Customer liaison.
QA Manager
Maintains all quality related procedures, Calibration
and record keeping of all inspection equipment.
Safety Director
All related safety programs, Record keeping as required
by OSHA.
Purchasing
Vendor qualifications, Job related materials, Consumable
supplies, Subcontracting, Expediting
Shipping
Safe and timely delivery of product, Maintain customer
packaging standards, Storage and inventory of completed
goods, All support UPS and carrier activity.
Receiving
Inspection, Count, Disposition of all incoming materials,
Stock rack maintenance, Receiving documentation accuracy
and trafficking.
Facilities Manager
Repair and maintenance of all existing equipment, Installation
of new equipment, Record keeping.
< Back to Top
2.0
Policy Review Agenda
2.1] Management Shall provide for the "annual"
review of all company policies in an effort to determine
their effectiveness. Approved changes and recommendations
are to be documented and filed until they become drafted
into the "revised" body of text. Changes
are to be distributed to all personnel, as required.
< Back to Top
3.0 Standard Operating Procedures
3.1] The Company shall produce and make available
to all employees, a set of "Standard Operating
Procedures". The range and detail of the procedures
will depend on the complexity of the work, and the
skills and training required to carry out the specific
activity.
< Back to Top
4.0
Document Control
4.1] A system shall be established and maintained
through which all "hard copy" customer communications
with regard to manufacturing requirements will be filed
and made accessable to management. The system shall
include;
- E-Mail
- Fax Transmittals
- Print Documents
- ECOs
- Formal and Informal quote response
- Purchase Orders
- Shipping Records
4.2] A system shall be in place to insure that proper
"rev levels" are available during manufacturing
and that obsolete drawings or information are removed
from circulation and clearly marked "obsolete".
4.3] A system shall be in place to track each separate
purchase order through manufacturing. Included shall
be; Job #, PO#, P/N, Rev. Level, Qty, Delivery Schedule,
and, any information regarding material requirements.
4.4] Daily production meetings will be held between
management and associated production personnel to ensure
"on-time" production of all work in process.
Customers are to be notified by the Operations Manager,
immediately, if there is a determination that a delivery
may be missed.
4.5] A system shall be in place for the tracking of
"Job" performances as they relate to each
individual run. This system shall include, but not
be limited to; Efficiency Ratings, Related Manufacturing
Problems, Improvements in design or technique.
4.6] Only documentation that has been "officially"
adopted by management shall be used. Employees shall
be properly instructed as to the use of all approved
documentation's. Copies of approved documentation's
shall be attached to this manual and made available
for review.
4.7] Employee responsibility with regards to documentation
will be clearly established through regular training
and periodic individual review.
< Back to Top
5.0 Purchasing
5.1] The company shall identify an individual
as "Purchasing Manager" to assume the procurement
responsibilities for the following;
- All Job related materials, including hardware.
- Subcontracted products and services.
- Consumable supplies.
5.2] The company shall establish a list of "Certified"
suppliers. Supplier certification will be determined
according to a rating system that will contain the following
criteria;
- Product quality
- Service dependability
- Price
- Corporate Social Responsibility
5.3] Manufacturing suppliers will be designated
as "Qualified". On-site inspections of supplier
facilities will be done as needed.
5.4] A list of qualified suppliers shall be maintained
and made available to Customers upon request.
5.5] All "job" related purchasing activity
shall be fully documented and maintained.
5.6] Purchasing Manager shall be responsible for
order placement, timely receipt of goods, and price
paid, including applicable freight charges.
< Back to Top
6.0
Inspection
6.1] Receiving Inspection and Testing. A system
shall be in place to ensure that the materials received
are correct and of good quality.
6.2] A system shall be in place to ensure that
"non-conforming" materials are clearly identified
and kept separate from "conforming" materials.
6.3] A system shall be in place that insures a
"first article" inspection and "sign-off"
during each new phase of all work in process. First
article sign-off sheets shall accompany each Job through
the manufacturing process. Records are to be filed
with closed jobs and made available for review at a
later date.
6.4] Individuals responsible for inspections shall
be clearly identified and available at all times during
regular manufacturing hours.
6.5] A final Inspection Report shall be completed
by designated individuals and filed with specific job.
A copy shall be provided to customers.
6.6] Final inspections shall be performed on "lot"
sample quantities of up to 100%. Quantities to be determined
by QA Personnel as required to ensure run accuracy.
6.7 A "Corrective Action Report" must
be completed by the Operations Manager with regard to
all "Customer Rejected Materials". A copy
of the report is to be kept on file and made available
upon request.
6.8] A system shall be in place for the review
and documentation of all "non-conforming"
materials. Materials that do not meet customer specifications
shall be identified, tagged, and stored, in a way that
will prevent them from being mixed with "conforming"
materials, until proper disposition can be determined.
6.9] All inspection equipment is to be calibrated
according to schedule using certification services
and/or techniques that are known to be accurate. Schedules
are to be based upon the individual instruments usage.
All equipment is to be tagged with the date of next
calibration and a log of this activity is to be maintained.
< Back to Top
7.0
Inventory Control
7.1] Valley Plastics shall assume full responsibility
for the proper handling and storage of all customer
supplied materials or tooling.
7.2] The company shall maintain a controlled inventory
of spare parts and tooling. Consigned materials and
tooling shall be properly stored and identified.
7.3] All completed product over-runs shall be
inspected, identified and stored in inventory in such
a way as to insure their separation from incomplete
or non-conforming materials.
7.4] All tooling, jigs, and fixtures shall be
stored and clearly identified with; customer name, part
number and latest rev level.
7.5] Parts are to be packaged and shipped in such
a way as to insure their safe and timely transport to
the customer's facility.
< Back to Top
8.0
Manufacturing Controls
8.1] Employees are to be properly trained as to
the level of manufacturing to which they are permitted
to perform.
8.2] Manufacturing employees shall be properly
trained in the utilization of all tools and programs
relevant to their job classification.
8.3] A system of communication shall be established
between management and manufacturing personnel that
facilitates the efficient and timely flow of information
regarding customer expectations.
8.4] Employees shall be required to operate in
a clean, organized fashion to insure the efficient transfer
of task responsibilities from one employee or department
to the next.
< Back to Top
9.0
Employee and Job Performance
9.1] As relevant to employee performance, all
employees are required to keep accurate records as to
time spent on a job.
< Back to Top
10.0
Employee Training
10.1] Each employee will be required to attend an
annual meeting to discuss the entire scope, including
revisions, of all Valley Plastics Policies, which is
to include this QA Manual. Records are to be kept of
those in attendance.
10.2] Employees are to be classified as to the level
of manufacturing at which they can operate. A clear
set of guidelines and expectations will be delivered
to each individual employee during his/her formal annual
review. Employee are expected to operate within the
standards set by these guidelines. Management shall
work continuously towards assisting employees with meeting
these expectations through both, "on the job training"
and, "outside education".
< Back to Top
11.0
Equipment Maintenance
11.1] Equipment use in the manufacturing process
shall be maintained as to adequately perform the task
required. A log shall be kept of all routing maintenance
operations.
11.2 In the case of "critical" pieces
of equipment where replacement parts have a typically
long lead time, spare parts inventory is required to
avoid the potential for excessive down time.
< Back to Top
12.0
Engineering Assistance
12.1] Programs shall be implemented that provide
for the efficient exchange of information that will
serve to improve product quality or reduce price. (
see "Cost Effective uses of Fabrication Technique")
12.2] The names and telephone numbers of "key"
engineering dept. contacts shall be maintained for each
customer.
12.3] Sufficient personnel will be made available
to assist qualifying customers with their engineering
needs, and shall include on-site visits to customer
facilities. We will also make available, sample materials
or technical data upon request.
< Back to Top
13.Employee
Awards Program
13.1] The company shall create a program for the
purpose of recognizing individual contributions that
have resulted in one or more of the following.
- An improved method or technique that drastically
increases productivity.
- Innovative ideas that, once adopted, have created
a positive environmental impact.
- Dedicated long term service or achievement with
regards to a "specialized" skill or effort.
< Back to Top
|